11-18-2003, 02:18 PM
|
#1
|
|
|
|
|
02-24-2005, 01:13 AM
|
#2
|
|
Hey Havik the link to the tech on 2.4 is not working. Trying to find info on the Ebrake section. Nothing on N-body or this site. You can pm me the link. Thanks
|
|
|
02-24-2005, 02:02 AM
|
#3
|
Senior Member
Join Date: Nov 2004
Location: Ankeny, Iowa
Posts: 253
|
They changed the website around on the j-body site. THIS is the new link.
http://www.ny-jbodies.org/forums/lib...ne/2.4/2.4.htm
__________________
<img src=\'http://www.supermotors.org/getfile/182743/fullsize/sig.jpg\' border=\'0\' alt=\'user posted image\' />
1999 Oldsmobile Alero
White
4 Door
74,000 miles
Twin Cam 2.4L
<span style=\'color:red\'>Let the modding begin!</span>
Current Mods: 2.3HO Intake manifold and Throttle body, Induction Dynamics intake, Unorthadox crank pulley, 15" Kicker CVR, Pioneer Premier headunit, Optima Yellow Top battery, and LED Undercar Lights
|
|
|
05-08-2005, 10:17 PM
|
#4
|
GX Member
Join Date: Apr 2005
Location: Holly Spings NC
Posts: 19
|
someone please tell me how i can turbo the hell out of my 2001 2.4 L
|
|
|
05-08-2005, 10:29 PM
|
#5
|
|
Quote:
Originally posted by roogz9@May 8 2005, 08:17 PM
someone please tell me how i can turbo the hell out of my 2001 2.4 L
|
Here's a start.
|
|
|
05-15-2005, 03:31 AM
|
#6
|
|
|
|
|
10-06-2005, 01:26 AM
|
#7
|
GX Member
Join Date: May 2005
Location: Phoenix AZ
Posts: 120
|
none of the links in this thread work except for the general quad4forums link.
|
|
|
10-06-2005, 07:52 PM
|
#8
|
Owner
Join Date: Nov 2003
Location: Joliet, IL
Posts: 19,932
|
__________________
72 442 "THE BEAST", 99 Alero - OSV Replica w/ original OSV parts, HURST Dual/Gate Shifter
Beware of the BackStabber
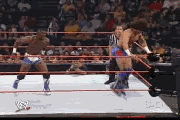
|
|
|
05-23-2006, 04:24 PM
|
#9
|
GL Member
Join Date: Dec 2004
Location: Toledo, Ohio
Posts: 397
|
Thanks I will be using those!
|
|
|
07-08-2007, 09:56 AM
|
#10
|
|
maybe its just me bieng an idiot. but i cant get any of the links to work. i judt need to know what the tranny is in my 01 2.4 auto.
|
|
|
10-19-2008, 04:11 AM
|
#11
|
GL Member
Join Date: Mar 2006
Location: PAX AMERICANA
Posts: 312
|
I'm going to post up the information that I can since all of these links are broken. It won't let me post up a lot of pictures though the website keeps saying I'm at my limit.
Once I get all the information up here a mod can delete this post and everything above it so that only the useful information is here.
Also, if someone can tell me how to post pictures on here without just linking them from another site I would appreciate it. I have a decent amount of technical drawings I could share, but I don't know how to do it other than through photobucket, and like I said, if they are on this server they will never go away.
I will add more information to everything listed below once I figure out the picture issue.
__________________
99 Alero 3.4l GLS - Totalled
95 Avenger ES - Sold
01 Alero 2.4l 5spd - Sold
06 Mazdaspeed 6 - Current Vehicle
Last edited by sburke : 10-19-2008 at 05:48 AM.
Reason: Adding another comment
|
|
|
10-19-2008, 04:19 AM
|
#12
|
GL Member
Join Date: Mar 2006
Location: PAX AMERICANA
Posts: 312
|
Disclaimer
First off, I can not claim this information. There are many other people who have put a great deal of effort into compiling this information. I would give them credit, but I do not know everyone who assisted in the original creation. In short, this is a repost of technical data that no longer exists on other sites.
Second. This is regurgitated information so use at your own risk. Aleromod and it's member's are not responsible for any damages or injuries that may result from your application of this information.
Finally, should you use this information to help you build your car, good luck and I hope you find it useful.
-sburke
__________________
99 Alero 3.4l GLS - Totalled
95 Avenger ES - Sold
01 Alero 2.4l 5spd - Sold
06 Mazdaspeed 6 - Current Vehicle
|
|
|
10-19-2008, 04:53 AM
|
#13
|
GL Member
Join Date: Mar 2006
Location: PAX AMERICANA
Posts: 312
|
Engine Mechanical Specifications (Sorry it's jumbled, it will not allow excel spdsht)
Application /Metric /English
General Data
Engine Type: Inline 4 Cylinder
Displacement: 2.4 Liter (146 CID)
Liter (VIN): T
RPO: LD9
Bore: 90 mm 3.54 in
Stroke: 94 mm 3.70 in
Compression Ratio: 9.5 to 1
Firing Order: 1-3-4-2
Lubrication System
Oil Capacity Without Filter Change 3-3/4 Liters 4 qts
When Changing the Oil Filter, Up to an Additional 0.946 Liter or One Quart of Oil may be Needed. Filter Type or Equivalent PF-44
Oil Pressure @ 3000 RPM 207 kPa 30 psi min.
Oil Pressure @ 900 RPM 69 kPa 10 psi min.
Cylinder Block
Cylinder Bore Diameter 89.994-90.006 mm 3.5110-3.5435 in
Out Of Round Maximum 0.010 mm 0.0004 in
Taper Maximum. Top to 106 mm (4.173 in) Down 0.008 mm 0.0003 in
Runout Rear Face of Block to the Crankshaft.
Center Line Maximum 0.07 mm 0.002 in
Cylinder Head
Cylinder Head Flatness
Maximum material that can be removed 0.076 mm 0.003 in
Do Not Resurface if the Measurement is Less Than 0.076 mm 0.003 in
Resurface 0.076-0.25 mm 0.003-0.010 in
Replace the Head if the Measurement is More Than 0.25 mm 0.010 in
Volume 58.9 cc-60.1 cc 1.5825 oz-1.6501 oz
Runout 0.05 mm 0.00196 in
Valve Seat Diameter Intake 34.066 mm 1.3412 in
Exhaust 27.048 mm 1.1436 in
Intake Valve Guide I.D. 5.921-5.941 mm 0.2331-0.2339 in
Exhaust Valve Guide I.D. 5.908-5.928 mm 0.2326-0.2334 in
Valve Stem to the Valve Guide Clearance Intake 0.024-0.070 mm 0.000986-0.00275 in
Exhaust 0.037-0.082 mm 0.00150-0.00320 in
Piston
Clearance in the Bore 0.019-0.051 mm 0.0007-0.0020 in
Compression Height 29.27-30.03 mm 1.180-1.182 in
Piston Diameter at 70°F (21°C) 89.957-89.973 mm 3.6203-3.6210 in
Piston Pin Bore I.D. at 70°F (21°C) 22.002-22.006 mm 0.8662-0.8664 in
Weight Less Pin and Rings 345 g +/- 6 g 12.075 oz +/- 0.1764 oz
Ring Groove Width, Top Compression 1.23-1.25 mm 0.048-0.049 in
Ring Groove Width, Second Compression 1.52-1.54 mm 0.0598-0.0606 in
Ring Groove Width, Oil 3.01-3.03 mm 0.1185-0.1193 in
Piston Rings
Compression Ring Width, Both 1.170-1.190 mm 0.0461-0.0469 in
Compression Ring Gap, Top 0.15-0.30 mm 0.006-0.012 in
Compression Ring Gap, 2nd Ring 0.30-0.41 mm 0.0119-0.0161 in
Oil Rails 0.025-0.65 mm 0.0098-0.0256 in
Compression Ring Side Clearance in the Groove,
Top Ring 0.040-0.080 mm 0.0016-0.0031 in
Second Ring 0.030-0.070 mm 0.0012-0.0028 in
Oil Ring Width 0.497-0.523 mm 0.01957-0.02060 in
Oil Ring Gap 0.399-1.40 mm 0.0157-0.0551 in
Piston Pin
Diameter 21.995-22.000 mm 0.8659-0.8661 in
Pin to Piston Clearance Loose @ 21°C (70°F) 0.002-0.011 mm 0.00007-0.00043 in
Pin to Rod Clearance 0.007-0.032 mm 0.00027-0.0013 in
Weight 109 g 4.0207 oz
End Play on Floating Pin 0.0-0.6 mm 0.00-0.0236 in
Crankshaft and Connecting Rod
Main Bearing Journal Diameter 60.031-60.010 mm 2.3634-2.3626 in
Width, Main Thrust Bearing Journal No. 3,
Including Fillets 27.837-27.913 mm 1.0959-1.0989 in
Out of Round Maximum 0.005 mm 0.0002 in
Straightness, Taper 0.007 mm 0.0003 in
Clearance 0.013-0.075 mm 0.0005-0.0030 in
Main Bearing Inside Diameter 60.033-60.071 mm 2.3635-2.3650 in
Crankshaft End Play 0.087-0.243 mm 0.0034-0.0095 in
Rod Bearing Journal Diameter 47.975-48.00 mm 1.8887-1.8897 in
Rod Bearing Inside Diameter 48.013-48.028 mm 1.8903-1.8909 in
Out of Round 0.005 mm 0.0002 in
Straightness, Taper 0.005 mm 0.0002 in
Clearance 0.013-0.053 mm 0.0005-0.0020 in
Rod Side Clearance 0.150-0.450 mm 0.0059-0.0177 in
Width 23.270-23.420 mm 0.9161-0.9220 in
Runout of Crankshaft at the
Flywheel Flange Maximum 0.03 mm 0.001 in
Runout of Crankshaft Maximum 0.025 mm 0.00098 in
Supported on Front and Rear Journals
Clearance to the Crankshaft Position Sensor 0.77-1.77 mm 0.0303-0.0697 in
Connecting Rod I.D. at the Small End 22.007-22.027 mm 0.8664-0.8672 in
Connecting Rod I.D. at the Large End 51.167-51.193 mm 2.0144-2.0154 in
Connecting Rod Width at the Small End 23.170-23.220 mm 0.9122-0.9142 in
Connecting Rod Width at the Large End 23.170-23.220 mm 0.9122-0.9142 in
Connecting Rod Width at the Large End
in the Same Engine, All Within 2 g 0.0705 oz
Connecting Rod Clearance to Piston P 0.007-0.031 mm 0.00027-0.0122 in
Rod Assembly Center to Center Distance 142.450-142.550 mm 5.6125-5.6164 in
Flywheel Fit 0.000-0.013 mm loose 0.0000-0.0005 in
Flange Runout Maximum 0.03 mm 0.00120 in
Stroke of Crank 94 mm 3.70 in
A.D. of Seal Diameter on Crank 81.96-82.04 mm 3.2210-3.2299 in
Runout of Seal Surface 0.05 mm max 0.002 in
Balancer Hub I.D. to Crank Snout O.D. Crank 33.00-33.03 mm 1.2992-1.3004 in
I.D. Balancer 33.00-33.03 mm 1.2992-1.3004 in
Timing Gear Fit to Crankshaft Snout 33.03-33.06 mm 1.3004-1.3016 in
Camshaft
Lobe Lift Intake 9.0 mm 0.354 in
Exhaust 8.8 mm 0.346 in
Journal Diameter No. 1 39.93-39.95 mm 1.5720-1.5728 in
Journal Diameter No. 2-5 34.93-34.95 mm 1.3751-1.3760 in
Camshaft Bearing I.D. No. 1 40.00-40.040 mm 1.5748-1.5764 in
Camshaft Bearing I.D. No. 2-5 35.00-35.040 mm 1.3780-1.3795 in
Journal Clearance 0.050-0.110 mm 0.0019-0.0043 in
End Play Clearance 0.025-0.225 mm 0.0009-0.0088 in
Lobe Taper 0.046-0.083 mm 0.0018-0.0033 in
On diameter in 14.0 mm 0.5512 in
Camshaft Housing
Lifter Bore I.D. 33.989-34.019 mm 1.3381-1.3393 in
Lifter O.D. 33.959-33.975 mm 1.3369-1.3375 in
Lifter to Bore Clearance 0.016-0.058 mm 0.0006-0.0023 in
Lip Seal Bore I.D. 49.975-50.025 mm 1.9675-1.9695 in
Lip Seal O.D. 49.975-50.025 mm 1.9675-1.9695 in
Cam Carrier Flatness 0.07 mm 0.0028 in
Bottom Maximum Within 100.0 mm (3.937 in) 0.025 mm 0.001 in
Valve Lifter
Clearance in Bore 0.016-0.058 mm 0.0006-0.0023 in
Valves
Valve Installed Height, All 24.86-25.62 mm 0.9787-1.0024 in
Valve Tip Above Spring Retainer, All 0.602-0.820 mm 0.0237-0.0323 in
Intake Valves, Valve Face Angle 46 degrees
Valve Seat Angle 45 degrees
Head Diameter 35.5 +/- 0.03 mm 1.3987 +/- 0.0011 in
Stem Diameter 5.921-5.941 mm 0.2331-0.2339 in
Overall Length 107.290 mm 4.2272 in
Stem To Guide Clearance 0.025-0.069 mm 0.0009-0.0025 in
Valve Seat Width 0.94-1.90 mm 0.0370-0.0748 in
Valve Seat Margin Minimum 0.25 mm 0.0098 in
Valve Face Runout 0.038 mm 0.0015 in
Valve Tip to the Groove Centerline 3.420 mm 0.1346 in
Exhaust Valves, Valve Face Angle 45.5 degrees
Valve Seat Angle 45 degrees
Head Diameter 28.870-29.130 mm 1.1366-1.1469 in
Stem Diameter 5.908-5.928 mm 0.2326-0.2334 in
Overall Length 108.17 mm 4.2586 in
Stem to Guide Clearance 0.038-0.082 mm 0.0016-0.0032 in
Valve Seat Width 0.094-1.90 mm 0.0037-0.0748 in
Valve Seat Margin Minimum 0.25 mm 0.0098 in
Valve Face Runout 0.038 mm 0.0015 in
Valve Tip to Groove Centerline 3.420 mm 0.1346 in
Valve Springs
Valve Spring Pressure Load
@ 36.5 mm (1.4370), Closed 223-247 N 50-55 lb
Load @ 26.98 mm (1.0622 in), Open 544-596 N 122-133 lb
Balance Shafts
Housing Flatness Maximum 0.076 mm 0.0030 in
Bore Roundness 0.025 mm 0.0009 in
Bearing Thickness 1.500-1.508 mm 0.0590-0.0593 in
Bearing I.D. 30.019-30.061 mm 1.1819-1.1835 in
Housing Bore 33.025-33.050 mm 1.3001-1.1801 in
Shaft Journal O.D. 29.950-29.975 mm 1.1791-1.1801 in
Journal Taper (Intentional Towards Counterweight 0.000-0.010 mm 0.000-0.0004 in
Journal Roundness Maximum 0.005 mm 0.0002 in
Bearing Clearance 0.044-0.111 mm 0.0017-0.0044 in
Gear Diameter over 2.5 mm pins 61.050-61.145 mm 2.4035-2.4073 in
Gear Backlash 0.008-0.086 mm 0.0003-0.0034 in
Chain Slack, With 6 lb of
pressure applied to the guide 1.0 mm 0.040 in
Shaft Groove Width 3.23-3.40 mm 0.127-0.134 in
Thrust Plate Thickness 2.945-3.045 mm 0.1159-0.1199 in
Endplay 0.185-0.455 mm 0.0073-0.0179 in
Oil Pump
Gerotor Pocket Depth 17.11-17.16 mm 0.6736-0.6756 in
Diameter 54.033-54.083 mm 2.1273-2.1292 in
Inner Gerotor Tip Clearance Maximum 0.15 mm 0.0059 in
Outer Gerotor Diameter Clearance 0.033-0.133 mm 0.0013-0.0052 in
Outer Gerotor Thickness 17.087-17.099 mm 0.6727-0.6731 in
Oil Pump Drive to the Driven Gear Backlash 0.23-0.51 mm 0.0091-0.0201 in
__________________
99 Alero 3.4l GLS - Totalled
95 Avenger ES - Sold
01 Alero 2.4l 5spd - Sold
06 Mazdaspeed 6 - Current Vehicle
|
|
|
10-19-2008, 05:06 AM
|
#14
|
GL Member
Join Date: Mar 2006
Location: PAX AMERICANA
Posts: 312
|
Fastener Tightening Specifications
Application Specifications Metric English
Balance Shaft Cover Nut and Bolt 13 N•m 115 lb in
Balance Shaft Driven Sprocket Bolt (left hand thread) 40 N•m + 45° 30 lb ft + 45°
Balance Shaft Housing Bolts 8 mm hex 10 N•m + 40° 89 lb in + 40°
Balance Shaft Housing Bolts 10 mm hex 15 N•m + 40° 11 lb ft + 40°
Balance Shaft to block Bolts 13 mm hex 25 N•m + 70° 18 lb ft + 70°
Balance Shaft to block Bolts 15 mm hex 53 N•m 39 lb ft
Balance Shaft to Block Bolts 18 mm hex 40 N•m + 60° 30 lb ft + 60°
Camshaft (exhaust) Rear Cover 14 N•m 124 lb in
Camshaft Position Sensor Bolt 10 N•m 89 lb in
Camshaft Sprocket to the Camshaft Bolt 70 N•m 52 lb ft
Connecting Rod Nuts 25 N•m + 80° 18 lb ft + 80°
Coolant Bleeder Valve Fully Driven, Seated , Not Stripped
Coolant Outlet to Cylinder Head 26 N•m 19 lb ft
Coolant Pump Cover to the Block 26 N•m 19 lb ft
Coolant Pump to the Coolant Pump Cover 14 N•m 124 lb in
Coolant Pump to the Timing Chain Housing 26 N•m 19 lb ft
Crankshaft Balancer to the Crankshaft 175 N•m + 90° 129 lb ft + 90°
Crankshaft Bearing Cap Bolts 20 N•m + 90° 15 lb ft + 90°
Crankshaft Position Sensor to Block 9 N•m 80 lb in
Cylinder Head Bolts Refer to Procedure
Cylinder Head Threaded Plug 26 N•m 19 lb ft
EGR Pipe to the EGR Adapter 26 N•m 19 lb ft
Engine Coolant Air Bleed Pipe 14 N•m 124 lb in
Engine Coolant Air Bleed Pipe Nut 42 N•m 31 lb ft
Engine Coolant Temperature Gauge Sensor to the Cylinder Head Fully Driven, Seated, Not Stripped
Engine Coolant Temperature Sensor to the Coolant Outlet 11 N•m 97 lb in
Engine Lift Bracket 96 N•m 68 lb ft
Engine Mount Bracket Adapter to Block Bolt Auto Trans 60 N•m + 60° 44 lb ft + 60°
Engine Mount Bracket Adapter to Block Bolt Manual Trans60 N•m + 60° 44 lb ft + 60°
Engine Mount (right hand side) to the Body Support Bolt 66 N•m 49 lb ft
Engine Mount (right hand side) to the Body Support Nut 44 N•m 32 lb ft
Engine Mount (right hand side) to the
Engine Mount Bracket Bolts 62 N•m 46 lb ft
Engine Mount Strut 100 N•m 74 lb ft
Engine Mount Strut Bracket Bottom Bolts 130 N•m 96 lb ft
Engine Mount Strut Bracket Front Bolts 66 N•m 49 lb ft
EVAP Canister Purge Valve Solenoid Bracket Bolt 8 N•m 72 lb in
Exhaust Manifold Brace to the Exhaust Manifold Bolt 56 N•m 41 lb ft
Exhaust Manifold Brace to the Oil Pan Nuts 26 N•m 19 lb ft
Exhaust Manifold to the Cylinder Head Nuts 15 N•m 11 lb ft
Exhaust Manifold to the Cylinder Head Studs 11 N•m 97 lb in
Exhaust Manifold Upper Heat Shield to the Manifold Bolts 14 N•m 124 lb in
Flywheel to Clutch Cover 20 N•m + 45° 15 lb ft + 45°
Flywheel to the Converter 66 N•m 49 lb ft
Flywheel to the Crankshaft 30 N•m + 45° 22 lb ft + 45°
Front Cover to the Timing Chain Housing 12 N•m 106 lb in
Fuel Pipe Bracket to the Camshaft Housing 15 N•m 11 lb ft +30°
Fuel Pipe to the Fuel Rail Nut 30 N•m 22 lb ft
Fuel Rail to the Camshaft Housing 26 N•m 19 lb ft
Ignition Coil and Module Assembly to the
Camshaft Housings 22 N•m 16 lb ft
Intake Manifold to the Cylinder Head Bolts/Nuts 24 N•m 18 lb ft
Intake Manifold to the Cylinder Head Studs 11 N•m 97 lb in
Knock Sensor 20 N•m 15 lb ft
Oil/Air Separator To Block Bolts 24 N•m 18 lb ft
Oil Dipstick Tube Bolt/Screw 8 N•m 71 lb in
Oil Filter Connector to the Block 29 N•m 21 lb ft
Oil Filter to the Block 3/4 to one complete turn after gasket contact
Oil Pan Bolts 24 N•m 18 lb ft
Oil Pan Bolts, Second Set 12 N•m 106 lb in
Oil Pan Drain Plug 26 N•m 19 lb ft
Oil Pan Studs 26 N•m 19 lb ft
Oil Passage Plug Bolt 30 N•m 22 lb ft
Oil Passage Plugs, 1/4x18 20 N•m 15 lb ft
Oil Passage Plugs, 3/8x18 30 N•m 22 lb ft
Oil Passage Plugs, Block 1/8x27 10 N•m 89 lb in
Oil Pressure Switch 14 N•m 124 lb in
Oil Pump Cover to the Oil Pump Housing - Short Bolt 10 N•m 89 lb in
Oil Pump to the Balance Shaft Housing - Long Bolts 12 N•m 106 lb in
Oxygen Sensor To Exhaust Manifold 42 N•m 31 lb ft
Powersteering Pipe to the Pump Nut 27 N•m 20 lb ft
Powersteering Pump to the Cam Carrier Bolts 26 N•m 19 lb ft
Rear Crankshaft Seal Housing to Block 12 N•m 106 lb in
Spark Plugs to the Cylinder Head 18 N•m 13 lb ft
Starter to the Block Bolt 90 N•m 66 lb ft
Tensioner to Tensioner Bracket Nut 54 N•m 40 lb ft
Throttle Body to the Intake Manifold 10 N•m 89 lb in
Thrust Plate to the Balance Shaft Housing 13 N•m 115 lb in
Timing Chain Housing to the Block Bolts/Studs 29 N•m 21 lb ft
Timing Chain Housing to the Camshaft Housings 26 N•m 19 lb ft
Timing Chain Tensioner to Housing and Block 10 N•m 89 lb in
Transaxle To Block Bolt 58 N•m 43 lb ft
Transaxle To Block Nut 66 N•m 49 lb ft
Transaxle To Block Stud 13 N•m 115 lb in
__________________
99 Alero 3.4l GLS - Totalled
95 Avenger ES - Sold
01 Alero 2.4l 5spd - Sold
06 Mazdaspeed 6 - Current Vehicle
|
|
|
10-19-2008, 05:17 AM
|
#15
|
GL Member
Join Date: Mar 2006
Location: PAX AMERICANA
Posts: 312
|
Sealers, Adhesives, and Lubricants
Application Type of Material GM Part Number
Balance Shaft Housing to Block Bolts Thread Locker 12345493
Cam Carrier Oil Cup Plugs Sealant 12346004
Cam Carrier Oil Passage Plug Sealant 12345382
Camshaft Lobes and Journals Camshaft/Lifter Prelube 12345501
Camshaft Sprocket Bolts Thread Locker 12345493
Chain Housing to Cam Housing Bolts Thread Locker 12345382
Coolant Air Bleed Pipe O-rings Coolant --
Coolant Outlet O-rings Coolant --
Coolant Temperature Sensor Thread Locker 12346004
Cooling System Coolant Sealant Pellets 3634621
Crankshaft Main Bearing Bolts Engine Oil --
Crankshaft Rear Main Seal Engine Oil --
Cylinder Block Drain Plug Sealant 12345382
Cylinder Block Oil Feed Plug Sealant 12345382
Cylinder Head Bolts Engine Oil --
Cylinder Head Coolant Plugs Sealant 12345382
Flywheel to Crankshaft Bolts Thread Locker 12345493
Front Main Oil Passage Plug Sealant 12345382
Front Oil Seal Chassis Grease 01051344
Heater H20 Control Assembly Valve Thread Locker 12346004
Injector O-rings Engine Oil --
Lifters Camshaft/Lifter Prelube 12345501
Lifters -- Store submerged Engine Oil --
Main Oil Passage Plug Sealant 12345382
Manifold Air Temperature Sensor Thread Locker 12346004
New Camshaft Engine Oil Supplement 01052367
New Lifters Engine Oil Supplement 01052367
Oil Filter and Rear Oil Passage Plugs Sealant 12345382
Oil Filter Plug Sealant 12345382
Oil Level Sensor Thread Locker 12345382
Pistons Varnish Remover 12345368
Pwr Steering Pump to Cam Housing Seal Sealant 12346286
Valves Varnish Remover 12345368
Water Outlet Valve Thread Locker 12346004
__________________
99 Alero 3.4l GLS - Totalled
95 Avenger ES - Sold
01 Alero 2.4l 5spd - Sold
06 Mazdaspeed 6 - Current Vehicle
|
|
|
10-19-2008, 05:34 AM
|
#16
|
GL Member
Join Date: Mar 2006
Location: PAX AMERICANA
Posts: 312
|
Getrag M86 5 Speed Transaxle
GM Part #: 22622126
Gear Ratios:
First: 3.58
Second: 2.02
Third: 1.35
Fourth: 0.98
Fifth: 0.69
Reverse: 3.31
Final drive ratio: 3.94Type:
Transverse Front Wheel Drive, Five-speed Manual Transaxle.
Maximum Engine Torque:
210 Nm
Maximum Gearbox Torque:
230 Nm
Fluid Capacity (Approximate):
1.7 L (Dry) = M86
1.8L (Dry) = MG3
Case Material:
Aluminum
B&M install directions
Tools needed:
10 mm socket
13 mm socket
Socket driver and extension
Sharpie marker
Utility knife or file
Long, thin straight slot screwdriver
Paper towels
Disassembly:
Step 1. Clean out stuff from your console, as you will be removing this.
Step 2. Four 10mm bolts secure the center console. One of the four is under a cover directly below the part of the dash that houses the radio. Use the straight slot screwdriver to gently pry the cover off. Remove the bolt. Bolt number two is under a trim piece behind the shifter. Gently pry off the trim panel (disconnect the power window switches) and set aside. Remove the bolt. The final two bolts are located inside the area under the armrest. This is where a long extension comes in handy. Remove the two bolts.
Step 3. To remove the center console, you will have to clear the shifter, parking brake handle, and another piece near the front that lies under the car. Unsnap the shift boot and pull the parking brake up as far as you can, as this will make it easier to clear both the brake handle and the shifter. Once you’ve cleared both pieces, gently move the console forward and lift to clear the hidden obstruction. Also, at this time you will want to remove the power wire for the second power outlet (cig lighter) if your car has one. Once you have the center console removed, place it somewhere out of the way.
Step 4. As you look at the shifter assembly, you will see two pieces that look like hydraulic rams that attach to the shifter. These are the shifter cables. Mark the position right in front of the gray and white clips as this positions your shifter’s gears. Release the cables from the shifter by gently prying up on the white and gray clips. They do not come up all the way but once you have moved them up a bit, you should be able to move the shifter around and the clips will slide over the cables instead of moving them.
Step 5. At this point, you need to remove the shift knob from the stock shifter. To remove it, you must twist and pull up on it hard. After the knob is removed, remove the four 13mm nuts that hold the shifter assembly in place. Also remove the two 10mm bolts that hold on the metal bar just above the front of the shifter assembly. Next, use your screwdriver to pry up on the two retainers that hold the cables to the shifter assembly. (these are two white cylinders attached to the front of the assembly) Once you have them dislodged, lift the assembly up and remove it. (this may take a little bit of wiggling the assembly around)
Step 6. Remove the fore-aft cable end from the bottom of the knob. This piece just pulls off.
Step 7. Remove the side-to-side pivot pin by pushing the slotted end through the base. (if you break this, it’s ok because b&m gives you a new metal pin to put in)
Step 8. From underneath the shifter assembly and using a the flat head screwdriver, carefully pry the three tabs of the plastic shifter retainer (looks like a round plastic ring that surrounds the “ball” of the shifter) toward the center of the base while pulling up on the retainer to disengage it from the base. This step takes a few tries. The tabs are hard to dislodge. Be careful not to use too much pressure and break the retainer.
Step 9. Remove the upper o-ring and then pull the shift stick out of the base. There is also a lower o-ring; save both of these as you will use them when you reassemble the shifter.
Step 10. Carefully disconnect the plastic main pivot housing from the shifter. This is the piece that surrounds the ball of the shifter.
Installation:
Step 11. Grease the main pivot point of the B&M shifter and snap on the plastic main pivot housing. (grease is supplied by B&M)
Step 12. Grease the nylon pivot cup of the B&M shifter. This is the small cap attached to the end of the arm that comes off the ball of the shifter.
Step 13. Place the lower o-ring into the shift base (if it came out… mine didn’t) and then insert the B&M shifter, followed by the upper o-ring. Make sure the pivot cup (the small cap from the last step) engages into the side-to-side actuating arm.
Step 14. Secure the shifter into the housing by snapping on the shift stick retainer. This is the point where, if you didn’t already remove the stock knob, you need to remove it because the retainer will not clear the stock knob or the other end of the shifter.
Step 15. Grease the supplied pivot pin and push it into the shifter base and secure it with the supplied c-clip. This is the piece referred to in step 7.
Step 16. Grease the lower ball of the shifter and snap on the fore-aft end cable. This is a little tricky to do, as the round end of the shifter doesn’t want to slide into the end cable. Push hard is the only advice I can give. Eventually, it will snap on.
Step 17. Reinstall the shifter assembly into the car and secure with the 13mm nuts. Make sure you get the cables back into the cable ends before you try to remount the assembly. Also, make sure all carpeting and insulation is cleared from under the shifter. I found it easiest to slide the cables back into the cable ends far enough that I could attach the cable retainers (white cylinders attached to the cables) to the shifter base. Then move the carpeting and insulation as best you can and line up the holes. Use a straight slot screwdriver to clear any carpeting or insulation that might be caught under the base.
Step 18. Position the white and gray clips to line up with the marks you made on the cables and snap them back down.
Step 19. Temporarily install the shift knob and test entry into all gears with the clutch pedal depressed. Apply a small dab of grease to the plastic interference “step” that blocks entry into reverse. (aka the reverse lockout) Make sure each gear can be smoothly and fully engaged before proceeding. This should not be a problem if you marked the cables. If need be, make necessary adjustments to the cable positions until each
gear smoothly engages. Remove knob.
Step 20. Replace center console. Just reverse the order of steps 1-3. Make sure to plug in your power windows and power outlet if applicable.
Step 21. Note: slight modification to the shifter boot frame may be required to give adequate clearance for the shifter while in reverse. Use the utility knife or small file to remove a small amount of the shift boot frame and then test before proceeding. Do not completely cut through the frame as it may no longer hold its shape or install correctly into the center console. I didn’t need to do this but you may.
Step 22. Affix the shift boot to the reverse lockout sleeve. Use the supplied tie wrap if needed then snap the shift boot into the center console. Another step I didn’t need. You may want to get a different shift boot depending on your tastes.
Step 23. Install the supplied rubber washer over the threads of the shifter and into the reverse lock out sleeve. Then place the supplied spring on top of the washer.
Step 24. Screw the knob onto the exposed threads. Then install the supplied o-ring onto the knob insert and press the insert into the top of the shift knob.
Step 25. Once again test the movement of the shifter into all gears making sure all can still be fully and smoothly engaged.
Step 26. Take the car for a drive and enjoy!
__________________
99 Alero 3.4l GLS - Totalled
95 Avenger ES - Sold
01 Alero 2.4l 5spd - Sold
06 Mazdaspeed 6 - Current Vehicle
Last edited by sburke : 10-19-2008 at 05:41 AM.
|
|
|
10-19-2008, 05:36 AM
|
#17
|
GL Member
Join Date: Mar 2006
Location: PAX AMERICANA
Posts: 312
|
2.3 Oil Pump Conversion For the 2.4 Twin Cam
Here is the how to for doing the 2.3 oil pump conversion, so that hopefully all those who search from hereon will find something solid.
The how to comes from Mantapart (thanks Tim) and it seems to work.
Parts Needed
2.3L Pump:
Crank Gear for the pump:
Windage Tray: 22536409
Baffle Stud: 22542521 x2
Baffle Bolt: 22540299 x2
Oil Pick Assembly: 22539133
Brace: 24570677
Bolt To Screen: 11516802 x2
Nut For Brace: 22535081 x2
Bolt Flange Head: 11516061 x2
Oil Pump Bolts To Block: 14050422 x2
Locator Pins For Pump: 22531530 x2
2.4 TC Crankshaft Modifications (Replacing the oil pump drive gears)
The 2.4L crank drive gear must be carefully heated and pressed or tapped off the crank. Be careful not to damage the crank surfaces or apply a lot of heat to the crank. The new oil pump drive gear should be heated and pressed back onto the crank. Use a brass hammer only if needed so you do not damage the teeth.
2.4L TC Block Modifications (These need to be done by a qualified machinist)
The oil passages to the pump must be re-machined to match the 2.3L pump. This operation must be done with the engine apart since it will require thorough cleaning when finished. Make a template from the right side of the oil pump that includes the bolt holes, oil passage and dowel pin holes. Lay it over the bolt hole on the block and carefully center and indicate the large oil hole center. This hole must be started and then drilled at an angle to intersect the horizontal oil passage that runs below it on the block. If you look from the back side of the block you will see where the passage pipe plug comes out. Draw a line on center with it and the hole center punch you have indicated and that is the angle the hole must be drilled. Drill the hole small and then increase drill sizes up to 9/16”. You will break through the casting and then drill into the oil passage casting. Make sure the final drill with the 9/16” bit is done slowly and smoothly, since you have to install the 2”x9/16” sleeve afterwards. Cool the sleeve and coat it with sealant. Gently tap it into the hole until it is flush with the block deck. Remove the oil galley plug to clean the passage and make sure the sleeve does not protrude into the oil passage bore.
Mount the pump up to the block and square it with the back of the block and snug it down gently. Take a small center punch and indicate the right side dowel pin hole into the block. Remove the pump and drill the hole to size #A machinist bit about 5/16” deep and then tap the dowel pin into the hole. Block the existing oil holes on the bottom of the 2.4L block: You must block the passages on the #3 and #4 main bosses on the bottom of the block, also. The larger angled hole can be tapped to a 3/8NPT (May require re-drilling to 37/64”) Remove the small round sleeve next to the hole first. And the smaller hole on the #3 boss needs to be drilled to a #R Machinist drill and tapped to 1/8NPT. The best is to use flush Allen pipe plugs and coat them with pipe sealant.
Install the pump on studs on #4 main bosses. A 14mm plug or short bolt can be installed in the other hole on the #3 boss. The sheet metal oil pickup holes will need to be slotted or you can carefully braze 2 small washers on it to line up with the studs that are installed on the #4 boss holes.
Fit the windage tray up – you will have to bend the left side up some to clear the thicker oil pan flange rail on the block. You will also have to enlarge the two holes at the studs to fit onto them. You will then have to indicate and drill two new holes for the windage tray front on the #2 boss flange area also. We suggest either a 3/8-16” coarse or 10mm x 1.5 thread bolts here, about ¾” (20mm) long.
2.3L Pump Modifications (The pump comes supplied with all other mounting hardware, etc)
The bottom boss on the oil pump must be ground down to clear the bottom of the 2.4 oil pan and the oil pickup may have to be moved up some to make proper clearance with the bottom of the pan. Make some trial fits with the pan and pump with the old oil pan gasket on the block to ensure proper fit. Some pans may require grinding and/or welding (aluminum) on the pan also for clearance. Make sure the pickup is not flat against the bottom of the pan.
__________________
99 Alero 3.4l GLS - Totalled
95 Avenger ES - Sold
01 Alero 2.4l 5spd - Sold
06 Mazdaspeed 6 - Current Vehicle
|
|
|
10-19-2008, 05:43 AM
|
#18
|
GL Member
Join Date: Mar 2006
Location: PAX AMERICANA
Posts: 312
|
Throttle Body FAQ
Throttle body flow measurements:
(flow ratings are at 7 in/HG of vacuum)
stock 2.4L (52mm) 240 CFM
stock 2.3L (56mm) 285 CFM*
bored 2.3L (60mm) 345 CFM*
* flow ratings based on Mantapart throttle body flow claims.
For comparison:
LT1 2x48mm @ 7" - 357 CFM
LS1 75MM @ 5" - 337 CFM
Ford 4.6L 2x57mm @ 3" - 357 CFM
2.0 Neon SOHC 52mm @ ?" - 283 cfm
engine CFM calculated for the 2.3L LG0
6800 rpm at 100% V.E. 276 CFM
6800 rpm at 110% V.E. 304 CFM
engine CFM calculated for the 2.4L LD9
6500 rpm at 100% V.E. 275 CFM
6500 rpm at 110% V.E. 303 CFM
engine CFM calculated for the 2.3L W41
7400 rpm at 100% V.E. 300 CFM
7400 rpm at 110% V.E. 330 CFM
The following contains excerpts from a CarCraft magazine article on carbs. This information can also be applied to picking the correct sized throttle body for your engine.
article can be found here:
http://carcraft.com/techarticles/56919/
The value of using CFM formulas.
"Textbooks tell us you can accurately select the proper carburetor size based on a relatively straightforward formula that takes into account engine displacement, max rpm, and volumetric efficiency (VE).
Plugging some actual numbers into the equation, what does it recommend for a 350 engine turning 6,000 rpm at 100 percent VE?
607.6 cfm?! Virtually no one—whether the original equipment manufacturer, aftermarket tuner, or racer—actually installs such a small carb on a high-performance 350. In the real world, everyone knows these engines make more power with larger carbs. Yet dyno-tests show the formula is an accurate reflection of an engine’s airflow needs. The equation breaks down as a realistic carburetor size selection tool because carburetor flow ratings (in cfm, or cubic feet/minute) are taken at an arbitrary vacuum drop—3.0-inches Hg for two-barrels; 1.5-inches Hg for four-barrels—and there’s no guarantee that, at max-rpm wide-open throttle (WOT), any given engine actually sees the theoretical vacuum drop for which the carburetor is rated!"
The breakdown of what the flow ratings on carbs and throttle bodies really amount to.
"On the other hand, if a carb really does pull 1.5-inch-Hg (or more) vacuum at WOT, it has become a restriction. The carb is actually too small to let the engine realize its maximum power potential. That’s because the greater the pressure drop (the higher the vacuum reading) across or through the carburetor, the lower the air density is inside the intake manifold and combustion chamber. Racers like to see no greater than 0.5 to 0.75-inch-Hg vacuum on the top end. But race cars have high-stall converters and steep rearend gears, and most of them are lighter than the average street car. Racers don’t mind recalibrating the carb on the spot for changing track conditions. They are unconcerned about low-end driveability. That’s why all-out racers, when not restricted by the rules, run huge carburetors—the bigger the carburetor, the lower the pressure drop across it at any given airflow.
It’s a different story for street cars and dual-purpose street/strip packages. For these combos, the limiting factor in carburetor size selection is on the low-end side of the fuel curve. Will it have good part-throttle driveability in the engine’s normal operating range? How will it drive in the winter, desert, and mountains?
As in life, so it is with carbs: Compromises are called for—a fine balance. Not too big because you’ll lose driveability. Not too small or the carb becomes a major bottleneck. For most hot, dual-purpose cars, pulling about 1.0-inch-Hg manifold vacuum at WOT, max rpm on the dyno isn’t far off. But there are no guarantees. It’s impossible to know for sure how a carb will perform in a vehicle based on how it did on an engine dyno. Every combo behaves differently; what works in a featherweight car with a manual trans and 5-series rear-gears ain’t gonna cut it in a 3,700-pound ride with a mild converter and 3.23:1 rear gears. As Grant puts it, “You’ve got to do lots of empirical work and go through lots of trial and error. It really takes thousands of carbs before you get an intuitive feel for what’ll work on a given application.”"
here are some general rules in the article that can be applied to throttle bodies:
• Higher rpm requires a bigger bore
• Higher horsepower requires a bigger bore
• Higher compression ratios require a bigger bore
• More ignition advance requires a bigger bore
• A manual-trans car can use a larger bore than an automatic-trans car
• Steeper FDR gears tolerate a bigger bore
• Lighter cars can use a bigger bore
• Heavy cars need a smaller bore
• Too large a cam for the application requires a smaller bore
• With an automatic-trans car, too low a torque-converter stall-speed for the application requires a smaller bore
• Mild FDR gears require a smaller bore
• Low compression requires a smaller bore
__________________
99 Alero 3.4l GLS - Totalled
95 Avenger ES - Sold
01 Alero 2.4l 5spd - Sold
06 Mazdaspeed 6 - Current Vehicle
Last edited by sburke : 10-19-2008 at 05:45 AM.
|
|
|
10-31-2008, 04:27 PM
|
#19
|
GL Member
Join Date: Mar 2006
Location: PAX AMERICANA
Posts: 312
|
In your installation manual you will be mostly dealing with the diagram on page 11, figure 11. To get to this on the car you must first remove the IDI cover on your motor (the part with 2.4L Twin Cam written on it).
Under that you will have a white ignition tower and a black and silver square looking module. Remove the tower from the IDI cover and you will see your coils. The wires between the square module "Power train control module" and your coils are the ones you will be cutting.
Just a suggestion....mark one of the white wires with a dot so you don't have to remember which one is which! I cut and soldered the wires, then covered them up with heat shrink tubing.
There is one brown wire which is your "ignition 12 volts", and 2 white wires which are your "triggers". What I did to tell them apart is to look at the bottom diagram on page 11, coming from your coil harness the far left wire is your brown wire "ignition 12 volts", the second wire over on both the diagram and the harness is your trigger 1, and the last one on the far right is your trigger 2.
You might have the cut part of the black piece that is on the white tower to feed all the wires out, but try to keep as much as possible because that keeps the wires from touching the control module, which gets extremely hot. Or you can drill a hole in the side of the white tower case, as I did in the picture above. Just be sure to feed the wires thru before you solder them!
Wiring
On the square module/plug side of the wires: Connect the 2 red MSD wires to the brown "ignition 12 volts" wire on the plug. Connect the white MSD wire to the middle white "trigger 1" wire. Connect the green MSD wire to the other white "trigger 2" wire.
On the coil side of the wires: Connect the 2 brown/orange MSD wires to the brown "coil (+)" wire going to the coils. Connect the brown/white MSD wire to the middle white "coil (-) trigger 1" wire. Connect the remaining brown/green MSD wire to the remaining white "coil (-) trigger 2" wire.
You have now completed the hardest part of the installation!
Completed towers
(shown with RK Sport spark boots installed)
If you want to change your spark plugs now is the time to do it since everything is all apart. If you are going to be running nitrous I would MOST DEFINITELY switch to a super copper plug, like NGK TR55, otherwise it is up to you.
All your have left to do is mount your DIS II box and to wire your pos and negative to the battery, and the theft deterrent and staging rev limiter if you decide to run them, otherwise cap them off and they will be fine.
Switch settings
N/A setup
SW1: S1-OFF, S2-OFF, S3-OFF, S4-ON, S5-OFF, S6-ON, S7-ON, S8-ON
SW2: ALL OFF
SW3: S1-ON, S2-OFF, S3-ON, S4-OFF, S5-ON, S6-OFF, S7-OFF, S8-OFF
Nitrous setups
2 degrees retard, for up to 50-hp shots
SW1: S1-OFF, S2-OFF, S3-OFF, S4-ON, S5-OFF, S6-ON, S7-ON, S8-ON
SW2: S1-OFF, S2-OFF, S3-OFF, S4-OFF, S5-OFF, S6-ON, S7-OFF, S8-OFF
SW3: S1-ON, S2-OFF, S3-ON, S4-OFF, S5-ON, S6-OFF, S7-OFF, S8-OFF
4 degrees retard, for 50-HP to 100-hp shots
SW1: S1-OFF, S2-OFF, S3-OFF, S4-ON, S5-OFF, S6-ON, S7-ON, S8-ON
SW2: S1-OFF, S2-OFF, S3-OFF, S4-OFF, S5-OFF, S6-OFF, S7-ON, S8-OFF
SW3: S1-ON, S2-OFF, S3-ON, S4-OFF, S5-ON, S6-OFF, S7-OFF, S8-OFF
__________________
99 Alero 3.4l GLS - Totalled
95 Avenger ES - Sold
01 Alero 2.4l 5spd - Sold
06 Mazdaspeed 6 - Current Vehicle
|
|
|
01-29-2009, 05:23 PM
|
#20
|
GL Member
Join Date: Jan 2009
Location: Fowlerville MI
Posts: 874
|
can anyone tell me where a good place is to get some motor mods?
|
|
|
Currently Active Users Viewing This Thread: 1 (0 members and 1 guests)
|
|
Thread Tools |
Search this Thread |
|
|
Display Modes |
Linear Mode
|
Posting Rules
|
You may not post new threads
You may not post replies
You may not post attachments
You may not edit your posts
HTML code is Off
|
|
|
All times are GMT -4. The time now is 05:26 PM.
|